Reducing Rotor Vibrations in Active Conical Fluid Film Bearings with Controllable Gap
Received 06 September 2022; accepted 09 December 2022; published 30 December 2022
2022, Vol. 18, no. 5, pp. 873-883
Author(s): Kazakov Y., Kornaev A. V., Shutin D., Kornaeva E., Savin L.
Despite the fact that the hydrodynamic lubrication is a self-controlled process, the rotor
dynamics and energy efficiency in fluid film bearing are often the subject to be improved. We
have designed control systems with adaptive PI and DQN-agent based controllers to minimize
the rotor oscillations amplitude in a conical fluid film bearing. The design of the bearing allows
its axial displacement and thus adjustment of its average clearance. The tests were performed
using a simulation model in MATLAB software. The simulation model includes modules of a rigid
shaft, a conical bearing, and a control system. The bearing module is based on numerical solution
of the generalized Reynolds equation and its nonlinear approximation with fully connected neural
networks. The results obtained demonstrate that both the adaptive PI controller and the DQNbased
controller reduce the rotor vibrations even when imbalance in the system grows. However,
the DQN-based approach provides some additional advantages in the controller designing process
as well as in the system performance.
Download File PDF, 6.01 Mb |
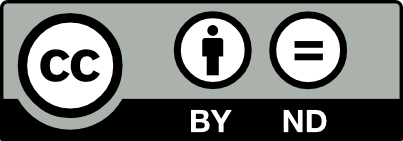
This work is licensed under a Creative Commons Attribution-NoDerivs 3.0 Unported License